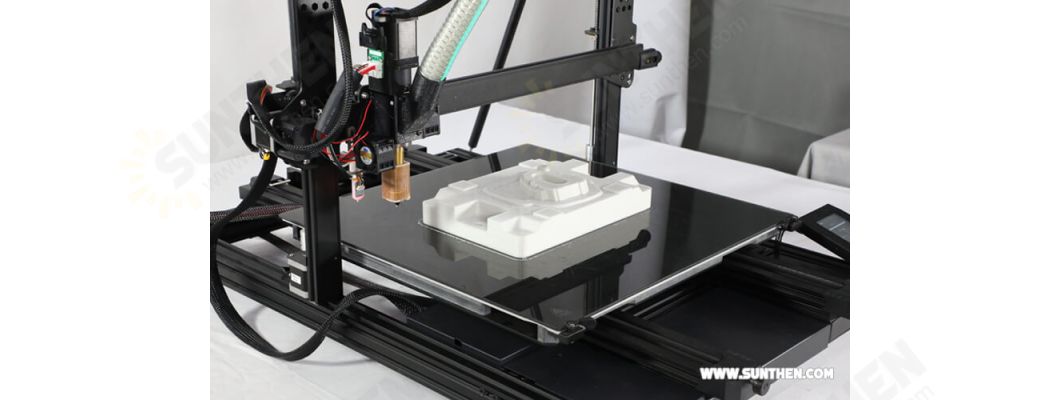
3D printing technology is revolutionizing the way people make items and bringing something that used to be impossible with traditional printing methods into reality. It offers convenience and efficiency along with a wide range of materials to choose from, enabling people to customize their creations as they desire. 3D printing technology is truly revolutionizing the way things are created today.
1. What is 3D Printer Technology?
3D printing technology is revolutionizing the way we make and create objects. It allows us to take a digital design, such as a computer aided design (CAD) file, and convert it into an actual 3D product using material such as plastic or metal. The process begins with creating a 3D model of the object on the computer, which is then broken down into layers that are printed one at a time in order to build up the object until it is complete. This technology has opened up new possibilities for product development and prototyping that were previously unavailable.
It uses a special process to scan, design and then prepare 3D objects in a layer-by-layer fashion. This allows for more complex geometries than traditional manufacturing techniques, and it also opens up the possibility for mass customization. With 3D printing, you can create almost anything from medical devices to toys and art pieces. 3D printers offer efficient production time, cost savings and greater convenience compared to traditional methods.
2. History of 3D Printer Technology?
1980s-3D printing technology was invented
In the 1980s, 3D printing technology, referred to then as Rapid Prototyping, was invented. The original purpose of this invention was to reduce the time it took for product development by providing faster prototyping. Initially, there wasn't much interest in 3D printing and its patents were abandoned. In 1981 Hideo Kodama of Japan filed a patent for a machine using UV light to cure photopolymers and three years later French inventors collaborated on a similar patent with General Electric deeming
1984s-3D printing technology develops rapidly
Charles Hull was a pioneer in the 3D printing industry, filing a patent for stereolithography in 1984 and founding 3D Systems three years later. His invention of the STL file format revolutionized 3D printing technology.
In the United States, the development of 3D printing technology accelerated in the same decade with the invention of Selective Laser Sintering (SLS) and Fused Deposition Modeling (FDM). Desktop Manufacturing Corporation and Stratasys were two major companies that advanced 3D printing, both founded during this time. The 3D printing industry underwent a transformation as it moved towards rapid commercialization. To meet the needs of large-scale automotive, consumer goods, health products and aerospace manufacturers, the first 3D printers were large and expensive. These printers provided industrial prototyping services for these companies.
1987s-3D printing technology start commercialized
In 1987, 3D Systems revolutionized the 3D printing industry by launching the first commercial-grade SLA printer. Five years later, Stratasys and DTM followed suit with the launch of their respective FDM and SLS printers. Finally, in 1994, Electro-Optical Systems (EOS) became the first company to introduce a metal 3D printer to market.
2000s-3D printing technology became affordable
At the start of the new millennium, companies involved in 3D printing faced fierce competition for profits. Thanks to developments in materials science and the expiration of various patents, 3D printing has become more affordable than ever.
Advances in 3D printing have revolutionized the manufacturing industry by making production components accessible to businesses of all sizes. Instead of relying on expensive machinery and equipment, now companies can quickly and easily create a wide variety of products using 3D printing technology.
3. How does 3D Printer Work?
The ISO/ASTM 52900 outlines the various categories for 3D printing, which are broken down into seven distinct groups. Each of these processes uses different methods and principles to print three-dimensional objects.
When 3D printing an object, there are a few factors that come into play to determine the time it will take to complete. These factors include the type of printing, the output size, the type of material used, desired quality, and the setup configuration. Depending on all these parameters, 3D printing can range from a few minutes to several days.
1) Powder bed fusion (PBF)
Powder Bed Fusion (PBF) is a 3D printing process that creates parts by selectively fusing specific areas of a powder bed layer-by-layer. This is done with the help of either an electron beam or a laser to heat and bind the particles together for precise building. Each layer is then recoated with fine powder before being scanned and the binding process is repeated until the part is finished. Depending on the material, sintering or melting processes may be used for better results.
As a 3D printing technique where a heat source scans and fuses successive layers of powder. This process creates a final volume with fused parts and the surrounding powder remains largely unaffected. The platform then ascends to let the user retrieve their completed build. Standard methods of powder bed fusion include selective laser sintering (SLS) and direct metal laser sintering (DMLS).
Selective Laser Sintering (SLS) is a 3D printing technology that uses lasers to fuse powder particles into layers. It offers the advantage of being able to create complex geometries without needing additional support structures. However, SLS parts are usually porous and have a grainy surface, requiring post-processing steps for finalizing the product.
Direct Metal Laser Sintering (DMLS) and Selective Laser Melting (SLM) are heat-intensive metal 3D printing processes. DMLS bonds particles at a molecular level, while SLM completely melts them together. These parts then require support structures which must be removed after printing using manual or CNC machining. Finally, the parts must undergo thermal treatment to relieve residual stresses.
Metal 3D printing techniques such as Direct Metal Laser Sintering (DMLS) and Selective Laser Melting (SLM) are capable of creating components with excellent physical properties that surpass even the base material used. The output is also known for a consistently high-quality surface finish. With these processes, you can use metals alloys and ceramics that can be hard to work with otherwise. However, these techniques come at a high cost compared to other 3D printing methods and have volume constraints that limit the size of the parts that can be produced.
2) VAT photopolymerization
VAT photopolymerization is a 3D printing technology that creates components layer-by-layer by using a light source to cure resin stored in a vat. This process can be split into two methodologies: digital light processing (DLP) and stereolithography (SLA). Both of these technologies offer tremendous accuracy and precision, making them ideal for creating intricate designs.
Digital Light Processing (DLP) and Stereolithography (SLA) are two 3D printing techniques. DLP uses a light source to flash an image of each layer onto a vat of liquid resin, then solidify them one at a time. SLA uses a single-point UV light source or laser to cure the liquid resin, forming the physical model from the bottom up. After printing, excess resin must be removed from the output and further exposed to light for increased strength.
For projects that need high-level dimensional accuracy, DLP (Digital Light Processing) and SLA (Stereolithography Apparatus) 3D printing methods are the best choice. They offer intricate details and a superior finish, making them optimal for prototypes.
These technologies are a great option for creating functional prototypes quickly, but they may not be suitable for outdoor use or due to the fact that the color and mechanical properties are likely to degrade when exposed to UV light. Additionally, support structures are often needed and can leave blemishes which can be removed through post processing.
3) Binder jetting
Binder Jetting is a process of 3D printing where the build platform is covered in a layer of fine powdered material such as polymer sand, ceramic, or metal. A print head then deposits adhesive drops to bind these particles together and create objects from these layers one at a time.
Binder jetting is a 3D printing technology that is used to produce metal, ceramic and polymer parts. The process involves applying a layer of powdered materials to a build platform before depositing droplets of binder material which binds particles together. This allows for large-scale production with an accuracy of up to +/- 0.05 mm. After the parts have been printed, thermal sintering or infiltration with low melting point metals like bronze must be done for metal parts and cyanoacrylate adhesive saturation for ceramic or full-color polymer parts are required for post-processing.
4) Material jetting
Material jetting is a 3D printing technique that is conceptually similar to inkjet printing. It uses one or more print heads to deposit layers of liquid material which are then cured before the next layer is produced. This process allows for intricate designs and elaborate details that would not be achievable with other 3D printing techniques. Additionally, material jetting can take advantage of support structures created using a water-soluble substance, allowing for easy clean-up after the building process is finished.
It is a highly precise process that can be used to create full-color parts made of different material types. While it offers great accuracy, it can be costly and the end product may be fragile and not last as long as desired.
5) Fused deposition modeling
Fused Deposition Modeling (FDM) is a 3D printing technique that uses heat and pressure to build objects layer by layer. A heated nozzle is used to feed a filament from a spool into an extrusion head. The extrusion head increases the temperature of the material, softening it before it is deposited in predetermined areas to cool and form each layer. When one layer is complete, the build platform descends and prepares for the next layer to be added.
FDM also known as Material extrusion, is a cost-effective process with low lead times, yet it's limited in terms of dimensional accuracy and finish. Post-processing is usually necessary to achieve a smooth finish, and the output is not well suited for critical applications as it tends to be weaker in one direction.
6) Sheet lamination
Sheet lamination is a manufacturing process that can use either ultrasonic additive manufacturing (UAM) or laminated object manufacturing (LOM). UAM utilizes ultrasonic welding to join thin metal sheets together at low temperatures and with minimal energy. It can work with stainless steel, titanium, aluminum, and other metals. Meanwhile, LOM uses alternating layers of material and adhesive to create the desired product.
7) Direct energy deposition
Direct energy deposition is a 3D printing technique that uses focused thermal energy, such as a laser, electric arc, or electron beam. This heat source fuses powder or wire feedstock horizontally to create layers which are then stacked vertically to build the desired part. It has the advantage of being able to work with a variety of different materials like ceramics, polymers, and metals.
4. Benefits of 3D Printing
3D printing is a revolutionary technology that has enabled us to create complex objects with astonishing accuracy and detail. It offers a range of benefits, including cost savings, faster time to market, and better customization options. It also allows for more sustainable production as materials are only used when needed. 3D printing has enabled businesses to produce complex parts more quickly, efficiently and accurately than ever before.
- Rapid prototyping: 3D printing enables you to prototype products quickly and cost-effectively.
- Customization: You can customize parts and products to meet your specific needs with 3D printing.
- High accuracy: The accuracy of 3D printed parts is often much higher than traditional manufacturing methods.
- Unlimited designs: With 3D printing, you can create virtually any shape or design imaginable.
- Cost-effective: 3D printing can significantly reduce the cost of producing individual parts.
- Time efficient: Complex parts can be printed in hours, instead of days or weeks.
- Eco-friendly: 3D printing reduces the need for hazardous chemicals used in other manufacturing processes.
5. How to Choose the Right 3D Printer for Your Needs
Choosing the right 3D printer for your needs can be a challenge. There are many different types available and each one offers its own unique features, such as the size of print area, resolution, and more. It is important to consider your budget, desired features, and desired materials when making a decision. Once you have found the right 3D printer for you, you’ll be able to create beautiful models with ease.
Before making a decision, it is important to evaluate all points of the issue. Here is a checklist of things to consider.
- Know What You Need: Decide what type of objects you are looking to print, from small detailed models to larger pieces with intricate designs.
- Researching printer specs: Get familiar with key terminology and features to ensure the printer meets your needs.
- Consider the materials: Consider what materials you will be printing with and find a compatible 3D printer.
- Budgeting: Establish a budget before shopping so you can decide on the best option for you.
- Consider Size: Choose a 3D printer that fits your space while meeting your printing needs.
- Budget-friendly options: Compare features and prices to find the best 3D printer for your budget.
- Ease of use: Look for printers that are intuitive and easy to set up, so you can get started printing quickly.
- Check reviews: Read reviews from other users to get an understanding of the pros and cons of different printers.
Conclusion:
Thanks to technology, there are now more printing options than ever to meet your needs. The new 3D printing technology offers convenience and efficiency that was never available before..
Are you in search of the perfect 3D printer for your project? Look no further than us. We have the expertise to provide you with sound advice so that you can make an informed decision. Reach out to us via comment or contact form and let's get started.
1 Comment(s)
This helped more than expected. It gave me more confidence.
Leave a Comment